Wedge User Days are now part of the Trimble Forestry User Conference
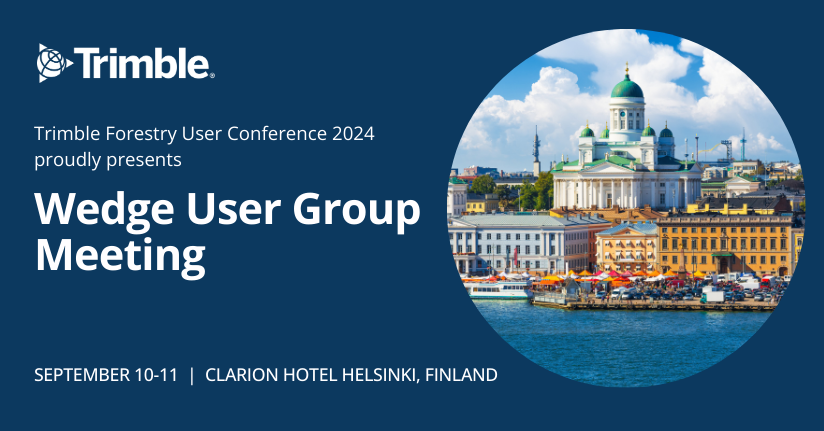
The traditional Wedge User Days will now be held for the first time as part of the Trimble Forestry User Conference. For Wedge users, there is a dedicated track called Wedge User Group at the event focusing on topics that will allow you to diversify and deepen your own use of Wedge.
The user conference is a two-day event. By participating, you will get to hear interesting user experience presentations from other Wedge users and receive tips and tricks directly from Wedge developers.
Time: September 10-11, 2024
Venue: Clarion Hotel Helsinki, Finland
More information and registration >>
Secure your seat today!
Note: All contracted Wedge users, please contact your Wedge sales representative for a promo code.
Major pulp producers in Latin America have high expectations for their process data analysis
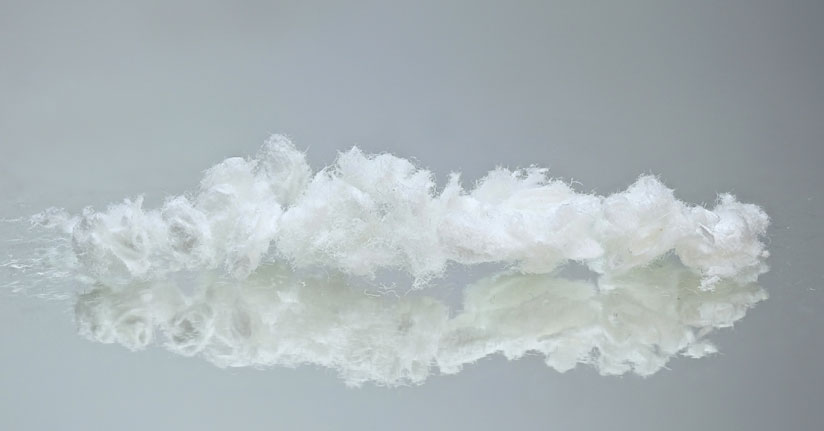
As of 2022, Brazil has been the world’s largest producer of pulp, and the industry continues to grow. Pulp is also the main export product of Brazil, with an annual value of USD 8.4 billion (2022).
To meet the high demands of the international market, the pulp and paper industries in Brazil are making investments in data analysis and management technologies. With a powerful data analysis tool, Wedge, companies like Klabin are able to better monitor internal processes, quality control and compliance.
The use of Wedge technology for data analytics is also bringing results to companies in other parts of Latin America, such as Arauco in Chile and UPM in Uruguay, who are among the largest producers and exporters of pulp in Latin America.
Read more in an article by Madeira Total (in Portuguese)
Arauco expands its Wedge use in Chile
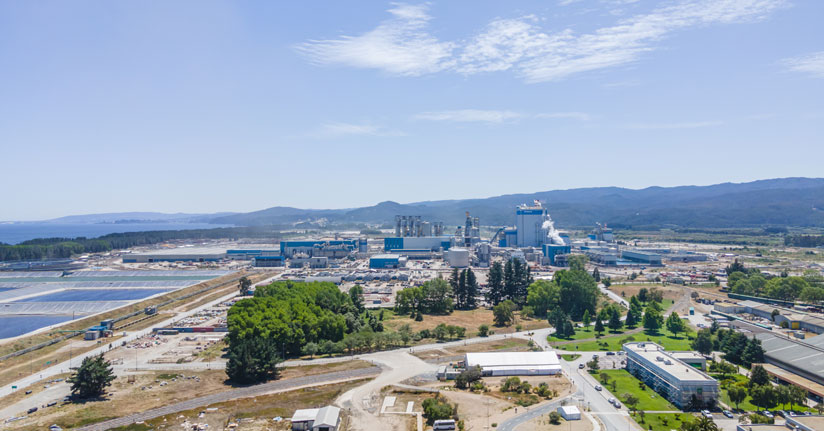
Global forest company Arauco strives for sustainable solutions and excellent energy efficiency in its operations. Arauco’s new production line in Chile is the newest line to implement this objective.
The history of this production plant goes back 50 years, with the installation of Line 1. Line 2 has produced radiata pine pulp approximately since 1990. Line 3 (initially called Project MAPA) is the largest eucalyptus pulp project in the world and Arauco’s most significant investment ever, and it has an annual production capacity of 2.1 million tons.
To achieve its high targets for sustainability, energy efficiency, and impeccable quality, Arauco has been relying on Trimble’s process data analytics system, Wedge, since 2018. Wedge has been used on two plants in Chile, and the new production line will also use Wedge for its process diagnostics.
With Wedge, Arauco can streamline its processes and reduce the time engineers spend on process data analytics. By quickly identifying the root causes of any production problems, Arauco can now minimize waste and ensure the consistent quality and smooth production of its products.
Arauco produces boards and wood that are used in furniture, construction, and packaging, as well as cellulose to manufacture, for example, papers, packaging materials, and diapers. Arauco’s products are available in more than 80 countries.
Let’s meet in 2024!
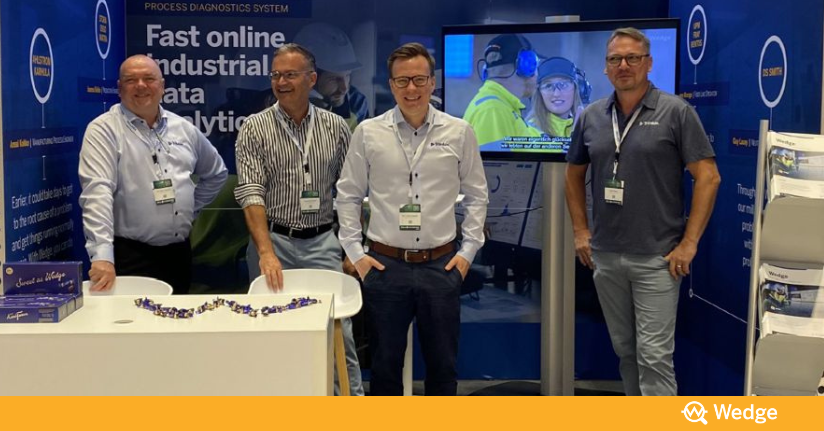
2024 will be a busy year for events. We hope to see you at least at one of these events:
- IMPS | Munich, Germany | March 19-21
- Pulp and Beyond | Helsinki, Finland | April 10-11
- Paper & Tissue One Show | Abu Dhabi, UAE | April 16-18
- Nordic Nuclear Forum | Helsinki, Finland | May 21-22
- Zellcheming | Wiesbaden, Germany | June 18-20
- MIAC | Lucca, Italy | October 9-11
See you soon!
Klabin expands its Wedge use to a new production line in Brazil
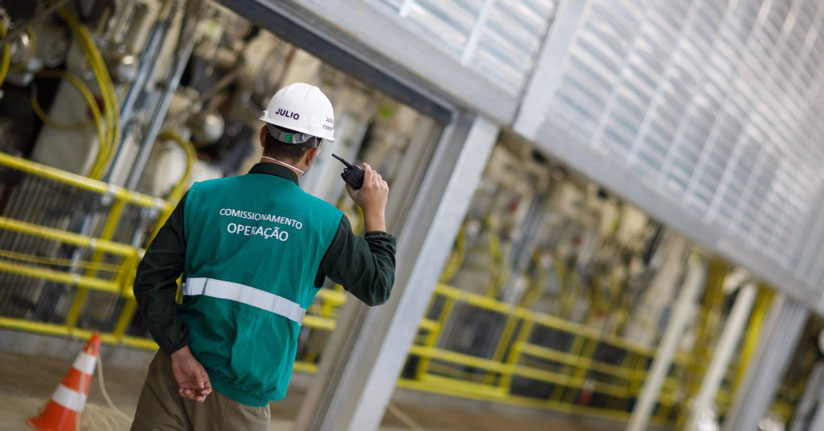
Klabin, Brazil’s largest producer and exporter of packaging paper and sustainable solutions in paper packaging, expanded its Puma Unit in Ortigueira, Paraná. This expansion, called the Puma II Project, includes two new paper machines, and represents an annual production capacity of 910,000 tons of paper.
The Puma Unit has been using Trimble’s process data analysis tool, Wedge, since 2021. Wedge has helped Klabin with advanced analyses to identify and correct deviations and optimize production processes. Based on user experience, Klabin has extended the use of Wedge to the new Puma II Project production line.
“In times when large volumes of data from production processes are made available online, the ability to interpret this information, combined with the speed and quality of decision making, are fundamental factors in maintaining and increasing plant performance. The ease of obtaining and processing data, in line with the robustness for processing calculations and advanced analyses, make Wedge a differentiated and fundamental resource for carrying out analytical activities,” says Elielson Batista, Process engineer at Klabin.
The Puma II Project was designed to become a global benchmark in sustainability, technology, and innovation, and it is aligned with Industry 4.0 principles. Efficient analysis of all process data is essential to achieving and maintaining the ambitious goals and objectives Klabin has for its operations.
Unleash the power of curiosity: The critical ingredient in data analytics success
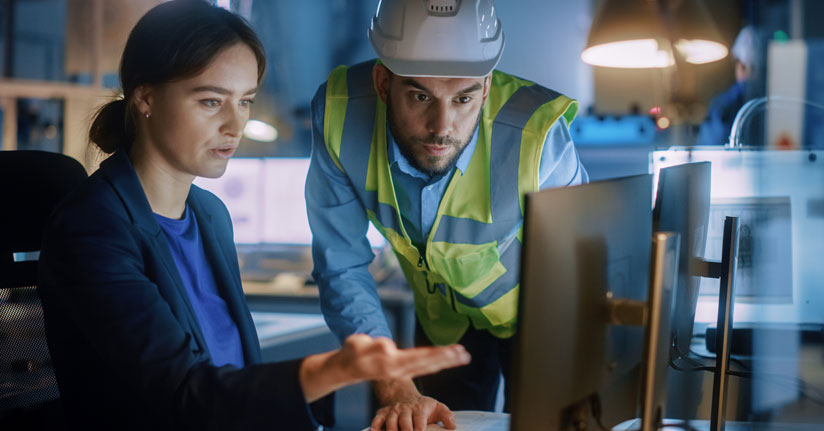
In the data-driven world, discussions focus on technology and buzzwords. However, it’s easy to lose sight of the unsung hero that distinguishes true leaders: curiosity.
Curiosity: Your gateway to data analytics excellence
Beyond the realm of technology lies the realm of human curiosity, a force that breathes life into data analytics. While technology undoubtedly plays a crucial role in enabling remarkable feats, it is merely a tool – a means to an end. The real magic happens when human curiosity takes the reins.
Unlocking the secret to value in process data analytics
In the vast landscape of process data analytics, a curious mind becomes the catalyst for transformation. It is this curiosity that drives individuals to collect and analyze data, construct and validate hypotheses, and ultimately translate discoveries into actionable insights. Technology can certainly enhance this cognitive process, making it more efficient and providing invaluable support, but it can never replace the sheer power of a creative and curious mind. In essence, without curiosity, no amount of technology can guide you towards true innovation.
The role of culture in fostering curiosity
We firmly believe that curiosity is a universal trait, ingrained to some degree in most individuals. However, its manifestation is profoundly influenced by organizational culture. A culture that nurtures and encourages curiosity becomes the breeding ground for true leaders. In contrast, organizations that stifle this innate curiosity find themselves playing catch-up, merely replicating what the leaders have pioneered.
The curious mindset: A prerequisite for leadership
To secure a leading position in any industry, cultivating a curious mindset is not merely an advantage but a necessity. Leaders who embrace curiosity as a core value embark on a journey of continuous innovation, setting the pace for others to follow. In a world where imitation is common, it is the curious leaders who stand out, charting new territories and leaving a trail for others to trace.
Navigating the future with curiosity
As we navigate the ever-evolving landscape of data utilization, let curiosity be your guiding light, illuminating the path to true leadership and innovation. In this journey, curiosity is not just a trait; it is a strategic imperative that propels us forward, ensuring that we don’t just keep up with the times but stay ahead of the curve.
Want more insights?
Our sales team is full of data analysis experts ready to help you. Learn more about Wedge process data analysis tool.
Wedge expands its language portfolio
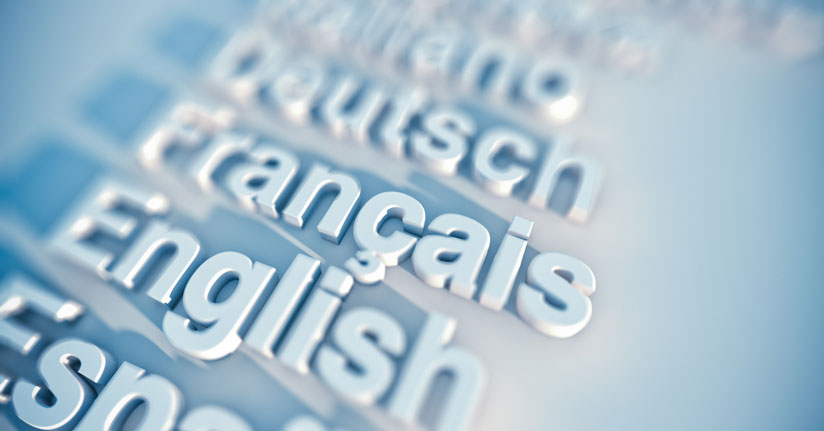
We are thrilled to announce that two new language versions of Wedge have been released this autumn! Joining the linguistic lineup are Italian and Norwegian, making Wedge even more accessible and user-friendly for a wider audience.
Wedge is now available in an impressive total of 11 languages. Whether you prefer expressing yourself in English, Finnish, French, German, Italian, Norwegian, Polish, Portuguese, Russian, Spanish, or Swedish, Wedge has got you covered.
This expansion reflects our commitment to breaking down language barriers and fostering global connections.
SharpCell selects Wedge to ensure consistent quality
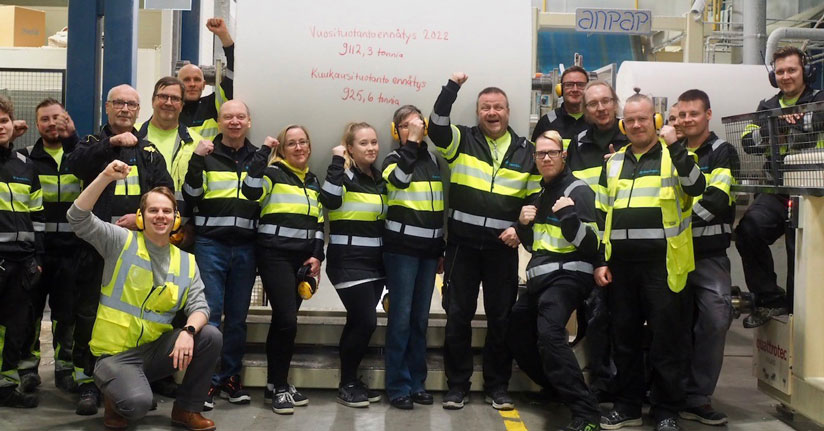
Finland-based SharpCell is one of the newest airlaid manufacturers in the world. They take pride in their consistent quality and reliable delivery of airlaid products for wiping, hygiene and personal care products, table top applications, household cleaning applications, baby care, and feminine hygiene.
To ensure consistent quality and trouble-free production processes, they have chosen Wedge for analyzing their process data. With Wedge, all process data can be utilized fast and easily to ensure zero waste, zero emissions, and minimal use of resources at all times.
“Wedge is a powerful piece of data mining software and a useful tool for understanding our production process on a more detailed level. The visualizing process and quality data help us widen our understanding of the current status of where we are on all organizational levels. Wedge is also a great asset in troubleshooting, and a tool for minimizing process variance. All this is supporting us in our main target, which is to be quality leaders in the airlaid segment.” says Production manager Eero Ollila, SharpCell.
5 practical ways to optimize your maintenance operations
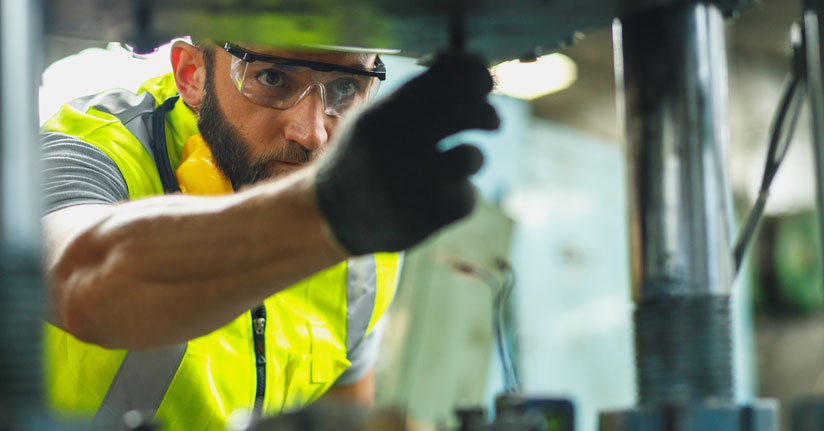
The cornerstone of modern maintenance may be predictive maintenance, but preventive maintenance is still very much in use, especially in industries where errors can be fatal. Whichever approach is used, data plays an essential part. Better use of data results in organisations being able to determine the state of the process and condition of equipment in order to estimate when maintenance should be performed. The goal? Fix potential defects before they result in failure or effect on process performance.
On-time maintenance is made possible by the integration of data utilization capabilities. At the end of the day, successful implementation is dependent not only on the organisation’s ability to turn data into accurate information, but also to further leverage the information to implement an efficient, scalable maintenance plan. Below are some tips, tricks and first-hand examples of how you can implement new data-driven strategies to enhance productivity, profitability and efficiency gains.
Leverage modern data analytics tools
Modern software tools can help you and your team analyze available data and translate it into accurate information that will help improve operations. They combine online data from various sources, including maintenance, condition monitoring, process control (DCS) and quality control (QCS) systems, to enable efficient data analysis. The data utilization can be visual, smooth and powerful, leading to enhanced production and easier maintenance development.
For companies pointed in this direction, the best case scenario is that all digital information is seamlessly integrated and users have a clear, overall picture of the process as a basis for better decision-making.
Five practical examples of data-driven maintenance
As you review these examples, keep in mind that the opportunities are limitless when high-quality data is combined with intelligent calculations and algorithms. For example, it is possible to estimate optimal maintenance timings, calculate sub-process performances or assess runnability risks.
#1: Begin with an equipment-level view
Often, when assessing the need for maintenance, it is worth going back to basics and begin by visualizing the data. Take a pump, for example. Collect and monitor the most critical measurements regarding the equipment’s operating condition (speed, current, vibration, temperature, etc.). Learn from that if the equipment behavior is normal.
#2: Start recognizing patterns
Study the dynamics of the process. You may notice that the relationship between, for example, the pump’s speed and current follows a certain curve. A deviation from that should potentially lead to an action by maintenance.
#3: Implement an SPC approach
The Statistical Process Control (SPC) data processing method has proven its power in several process industry areas. SPC is often used within Six Sigma initiatives to provide a factual base for the measurement type of methodology of process improvement, whether such a process is in relation to a production process or a service process.
SPC limits are also regularly utilized by maintenance teams. Deviation from the limits should potentially trigger an event-driven maintenance action.
#4: Compare process condition changes
Process conditions such as equipment setup, process control strategy, used raw materials and required properties of the final product are constantly changing. Studying the process changes provides a great way to learn about the process. On Trimble’s Wedge, for example, this can be done with the annotations or notifications to contextualize data.
The maintenance team might want to compare process variables before and after maintenance activities such as pump or valve replacement. For example, what changed in the data when we replaced a pump, and what can we learn from that? Is it possible to use this new information to schedule the next pump change more accurately?
#5: Study control loop performance
A modern production plant has a production control system and thousands of control loops that ensure production efficiency. Control loop performance is one of the automation maintenance team’s biggest headaches because poorly functioning control loops can cause serious deviations in product quality or profitability.
In order to evaluate control loop performance, combine control loop set points, controller outputs, measurements and state data. By analyzing the averages, deviations, maximums and minimums of the factors, it is possible to determine bottlenecks, dead loops, broken measurements and deviations easily.
In the end, remember that it’s not about how much data is collected, it’s what you do with the data. While most modern production operations generate significant amounts of data, the most successful ones are leveraging it to drive the business forward.
Want more insights?
Our sales team is full of data analysis experts ready to help you. Learn more about Wedge process data analysis tool.
UPM expands its Wedge use to new mill in Uruguay
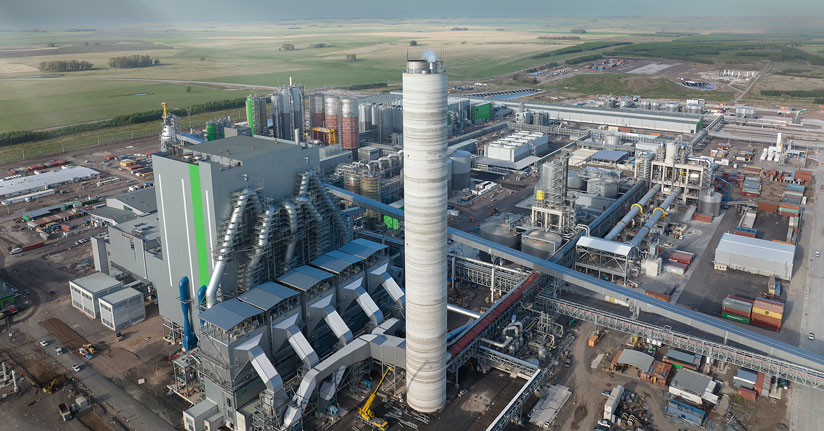
Forest company giant UPM has opened a new factory in Paso de los Toros, Uruguay with the capacity to produce 2.1 million tons of eucalyptus pulp annually. The mill incorporates the latest and best technology available and represents the very best in modern factories. It is energy efficient with minimal environmental impacts and optimized maintenance.
Wedge is Trimble’s process data diagnostics system that will help UPM Paso de los Toros to achieve and then maintain the highest standards of performance by enabling faster and better data-driven decision making. Trimble’s Wedge will result in reduced waste, mitigated risks and increased productivity at the new mill.
Choosing Wedge as its main tool for process diagnosis and monitoring was easy, since UPM’s first mill in Uruguay, Fray Bentos, has been using Wedge since 2019 and the results have been convincing. It is seamlessly integrated with the different systems that provide process data throughout the factory and is actively and widely used by operators, engineers, supervisors and process coordinators. UPM Fray Bentos also uses Wedge at the management level, with dashboards that summarize important steps in the process.