Steel manufacturer Outokumpu is advancing the digitalization of production at its research center in Tornio, Finland. The objective is to support production and incorporate excellent quality with the production parameters. Researchers and development engineers at the Tornio steel mill use the Wedge process analysis tool in their work.
“We purchased Wedge while the ferrochrome smelter was being built. It has brought us environmental reporting benefits and helped us with production inspections as well as management of water volumes. The program is used for monitoring various materials and deviations in power flows too. It is a good tool for research and development work and for examining ad hoc ideas and situations,” says Juha-Matti Pesonen, R&D manager at the Tornio works.
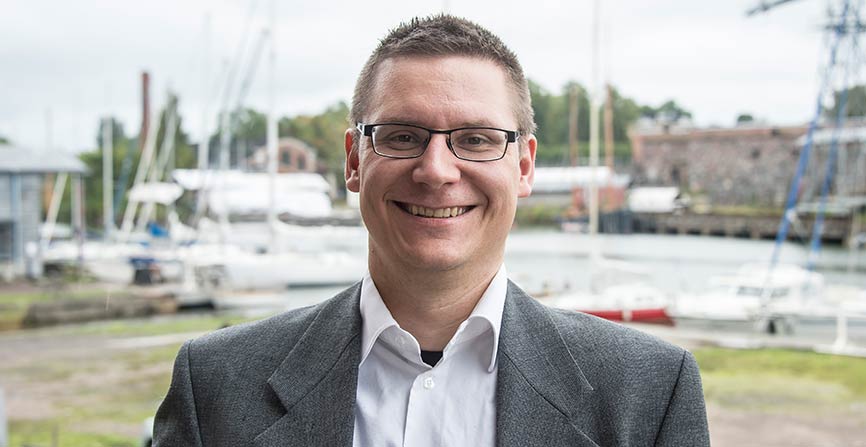
The use of Wedge has expanded from the ferrochrome smelter to production in the continuously active smelting operation. “Wedge has helped make work easier for the employees. Other opportunities exist also, but we are allowing the use of the tool to grow organically and gradually,” Pesonen adds.
Process with both continuous production and batch-run periods
Outokumpu is a leading producer of stainless steel globally, with a crude-steel production capacity of 3.1 million metric tons per year. The company produces stainless steel at its facilities in Finland, Germany, Sweden, Great Britain, the USA, and Mexico.
“A special characteristic of our production is that our process includes both continuous production and batch-run periods. When reviewing data, we can examine batch production details relative to the data from the continuous process. Therefore, the batch production tool of Wedge is extremely useful for us,” says Pesonen.
Improved user experience
According to Pesonen, experienced users of the process analysis tool can get more out of it, since they are familiar with production and are able to view the data from multiple angles and to visualize things. Also, the functionality of the program has now been simplified, and the program’s menu system has been streamlined.
Sustainability with optimized processes
Customers’ requirements pertaining to quality have increased, so production is focused on high quality. Today, the perspective of sustainable development is another highly important factor for both customers and investors.
Stainless steel is fully recyclable and withstands reprocessing well. Its constituent substances can be reused countless times in the production of new stainless steel.
Recycling and a long product life cycle are key elements in Outokumpu’s sustainability philosophy.
“According to one view, optimized processes also reduce the need for energy. We consume energy because our production process requires it, but our ongoing objective is to develop the operations such that we reduce consumption,” says Pesonen.
Wedge helps to detect deviations
According to Pesonen, Wedge has provided the company with cost savings by helping personnel detect deviations in the day-to-day processes and address issues rapidly.
He says, “The researchers can figure things out quickly, and Wedge has helped them identify factors that slow down production. The tool also makes it easy to visualize matters and to detect deviations in routine operations at the mill. The more you use the tool, the more benefits it provides. And the user events are always another valuable source of information and of new perspectives on one’s experiences with the tool.”
Want to learn more? Contact our sales team