Comprehensive production efficiency and customer benefits. This sentence sums up the idea behind the OPE concept of the Andritz technology company. The OPE concept is to raise plant’s Overall Production Efficiency.
Andritz is a globally leading supplier of plants, equipment, and services for hydropower stations, the pulp and paper industry, the metal working and steel industries, and for solid/liquid separation in the municipal and industrial segments. Other important fields of business are animal feed and biomass pelleting, as well as automation, where ANDRITZ offers a wide range of innovative products and services in the IIoT (Industrial Internet of Things).
Intensive dialogue with the customer and a focus on the big picture are key, whether the matter at hand is individual spare part deliveries, repairs, or enhancements to the customer’s equipment. Trimble’s process analytics tool Wedge is an unparalleled assistant in this dialogue.
It is a great advantage if the customer already uses Wedge. Since we both use the same tool and view the same parameters, we can be sure that we speak the same language, says Jari Kapanen, OPE Product Manager at Andritz.
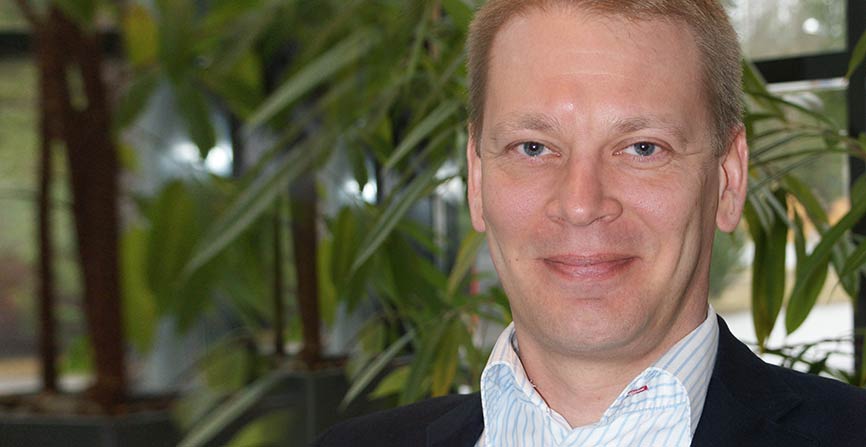
A clear operating method
Andritz introduced the OPE concept in its operations in Finland in 2003. The company’s main customers are pulp mills. The operations have gradually expanded to Chile, Russia, and Austria, where the company is headquartered.
“Contract customers give us positive feedback on our structured method to operate and develop processes. The benefit gained by the customer is always a top priority in the process. Good end results are not achieved without dialogue, Kapanen says.
A development team with members from the organisations of both the customer and Andritz is usually established for the cooperation. The objectives are defined together, and if the customer’s focus shifts along the way, they are adjusted flexibly.
“For example, the price of pulp fluctuates cyclically. During the high season, the product line capacity must be maximised and the costs must be managed. Therefore, we are fairly deep inside the customer’s core business operations.
A tool for tough situations
Wedge has helped the Andritz team solve a number of difficult issues at the mills. According to Kapanen, Wedge offers good usability and is well suited as a tool for process specialists.
“Today, a lot of information is available and gathered, but what is also needed is tools for data mining and analysis. Wedge offers a good reporting feature, and an effective summary report is important when solving problems. When a report indicates a deviation, the issue is easier to address.”
Wedge offers a good reporting feature, and an effective summary report.”
Kapanen has been using Wedge continuously since 2014, but bumped into the tool for the first time while studying. The process analytics tool is being used in many customer organisations.
“When you are looking for the fundamental reason for an issue in the production process, Wedge is really good at listing candidates. When a customer is also already using Wedge, we can compare our production reports with their and draw conclusions regarding the problem. This enables us to spend time on actual work instead of on troubleshooting.”
Savings in the production process
At the Stora Enso Veitsiluoto mill, Operations Manager Pasi Pigg uses the Wedge process data analysis tool almost daily. He plots a trend and draws up diagrams based on the information received.
“Preprocessing of data is a handy feature, and making one’s own calculations is relatively easy. There is not much time to prepare in-depth analyses while you work, but Wedge does all that for me quickly and effectively, Pigg says.
Preprocessing of data is a handy feature, and making one’s own calculations is relatively easy.”
Different departments at Veitsiluoto have been partnering with Andritz for approximately three years. According to Pigg, cost effectiveness and production efficiency have improved. The runnability of the boiler has improved and washing loss has decreased. This provides cost-savings in the bleaching process and in the usage costs of replacement chemicals. Energy savings have also been achieved at the evaporation plant.
“The development resources available at the mills have decreased, so the experience and insight offered by an external partner help us gain a better understanding of our in-house processes. Systematic OPE activities have had a positive impact on the company’s operations.
A self-sufficient unit
The Veitsiluoto mill produces 952,000 tons of paper per year. Two production lines manufacture fine paper and one makes coated magazine paper. Pulp generated by the company’s own mill is used directly as raw material for the company’s paper machines.
“We also operate our own sawmill, which produces 160,000 solid cubic metres of sawn timber per year. Sawmill chips are used in pulp production, whereas bark and sawdust are used for energy. Running the daily operations of a large mill integrate is so much work that research and development activities easily take a backseat. Luckily, we have Wedge and the OPE activities to assist us, Pigg says.”
Want to learn more? Contact our sales team